山东一然锻造炉锻造设备知识
信息来源:原创 作者:山东一然 发布时间: 浏览量:183
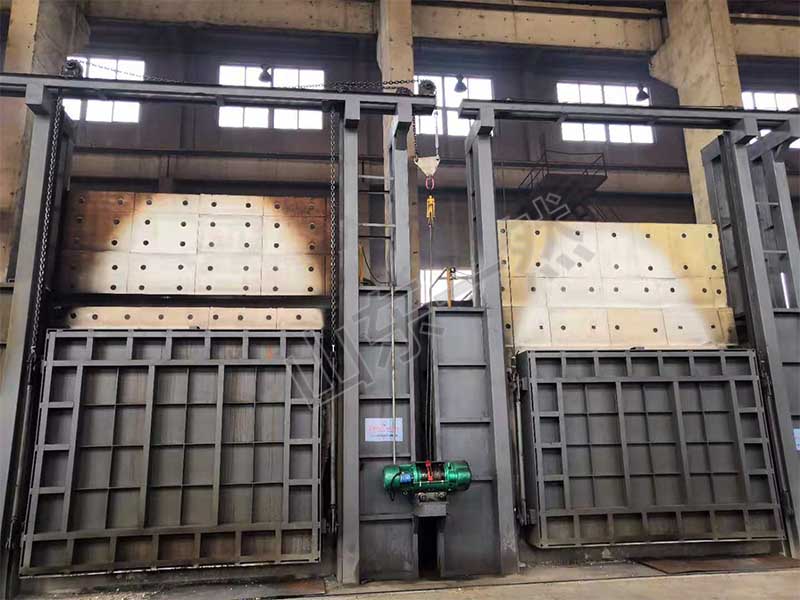
1.1 老式锻锤的改进
古老的锻锤是各种锻压机器的先驱,至今仍在我国锻造生产中占有数量上的优势。其中锤类设备最常用的为蒸气----空气锤,这类锤主要使用蒸气作为工作介质,由于其能量利用率太低(3%左右),工作时产生巨大的噪声和地基振动,促使人们想方设法对其进行改造。50年代,曾生产过系列的具有各种打击能量的双向对击锤,同时,人们对振动介质,材料选用和基础抗震进行了许多研究和改进,但总体效果不理想。60年代,人们开始研究以电动机驱动的液压系统代替老式锻锤的蒸气或压缩空气动力源,这种蒸汽锤的能量利用率可达75%,又因其在机身上设置了液压反弹系统,使整个设备锻造时对地基的振动大大减少,而生产效率与原来相当。经过70--80 年代尝试和引进改进,较受欢迎,但其工作噪音的问题仍未得到解决。山东一然天然气锻造炉跟随时代发展,把节能增效环保做好,是时代的产物,更是热销产品。
1.2 螺旋压力机
摩擦螺旋压力机是中国五六十年代的主要锻压设备之一,总体数量很大,与蒸空锻锤相当,几乎在每一个中、小型锻造车间里都由它承担着小批量模型锻造的生产任务。这种压力机在很多方面弥补了锻锤的不足,而且投资较小,我国磨擦压力机的最大公称压力达到35000KN。
虽然这种机器的名称和外型与锻锤差异很大,但就其作用于金属塑性变形的原理来讲二者是基本相同的。因此它同样有着效率低、能耗大的缺点。又因为它的特殊力能转换关系和整体框架式结构,实际工作中的打击力经常超载,机架、螺杆断裂的事故屡有所见,模具寿命也受到影响,人们采取了增加过载保护、更新操纵机构等措施,但并未达到预期效果。
70年代末,国外对传统摩擦螺旋压力机的结构进行了重大变革,把摩擦和飞轮的运动状态及主从关系互相调换,并应用了大量现代的机、液、电、计算机技术,出现了新型螺旋压力机。我国于90年代初制造出同类产品,现已有十余台达到国际先进水平的国产离合器式螺旋压力机投放市场。这种压力机不仅高效、节能,而且有效行程很长、可调,打击力和输出能量都是可以预选的,几乎集各种传统通用锻压机器之所长,但因它的技术含量较大,在使用和维护方面尚有待于人们的适应,其造价较高也需要企业有相当的经济承受能力。无论如何,这种新型螺旋压力机的优点是肯定无疑的,它也许会成为通用锻压设备的更新换代产品。
1.3 机械锻压机
加热、成形和精整三种设备构成模锻生产的基本单元,即所谓的“机组”。最简单的、也是最初始的模锻机组应包含加热炉、模锻锤、切边压力机各一台,若三者之间再用简单的输送机械联系起来,就形成各种现代锻造生产线的雏形。
50年代热模锻压力机就在中国的模锻机组中出现了,60年代筹建一个大型汽车制造厂曾用它完全取代了模锻锤。但相对于模锻锤来讲,它的造价是十分昂贵的,通用性较差,对工艺设计、下料精度、模具安装、设备调试等环节的要求都很高,因此多年来的应用都不很普及。锻锤和摩擦压力机的工作原理是较为简单的能量转换关系,即锻压机械把其执行部件从高速运动中所获得的动能转化为金属塑性变形的位能。热模锻压力机则与此不同,它主要是由刚性连接的机械传动机构发出强制压力克服变形阻力,使金属在准静态下塑性变形。依照这种原理工作的专用机械也很多,例如水平锻造机、多工位镦锻机、辗环机、弯曲机等。
1.4 电液锤
近10年来,我国在电液锤研制方面也取得很大发展,主要表现在传统蒸汽锤、空气锤、换头改造上。即采用电液传动装置了代原有锻锤的气缸及动力站!保留原有机架、砧座。安阳锻压机械公司利用这种技术为数十家企业改造1--3t传统蒸汽锤和空气锤10余台.取得了较好效果,能源利用率由2%提高到20--60%除换头外,电液锤整机的研制仍处于发展阶段,居于德国Lasco公司第2代产品发展水平上,属于液气锤,全液压锤研究和制造正在起步。
1.5 液压机
液压机的结构特点使其易于获得较大的工作压力、行程和空间;工作压力和工作速度可根据需要进行调整,且平稳,无冲击。其不足之处是生产效率比较低,活动横梁下死点不易控制准确。我国液压机设计制造技术与国际水平相当,第一重型机械集团、第二重型机械集团公司均可制造12000t液压机。我国拥有10000t级大型液压机数量已跃居世界第3位。为了提高液压机的使用效率,国外液压机制造商把目光放在锻造液压机的技术改造上,主要对液压系统和控制系统的改造。在这方面德国SPS公司,德马克公司积累了不少成功经验。液压系统采用现代的先导阀,手工操纵改用计算机控制$改造后液压机具有与快锻机相同的控制精度和性能。
二、发展趋势
2.1 自由锻锤的发展趋势
自由锻锤发展趋势就是大型化和成套化。过去由于制造水平的约束,我国双臂自由锻锤的最大规格只有5吨,单臂自由锻锤的最大规格只有3 吨。目前,安锻公司已经开发出8 吨双臂自由锻锤和5吨单臂自由锻锤,下一步还将开发出10吨双臂自由锻锤和8吨单臂自由锻锤。另外一个趋势就是成套化,根据自由锻锤的配套要求,成功开发了系列带锯机、系列操作机和系列装取料机。用户可以根据不同的锻造工件购买相应的成套自由锻设备。
2.2 模锻锤的发展趋势
模锻锤是模锻车间使用范围最广泛的设备,它的主要特点是成型速度快、金属流动性好、锻件质量高。因此,特别适用于薄壁零件的锻造成型,但是普通模锻锤打击能量不能精确控制,锻锤的操作者是靠听模具打靠声音来判断锻件是否打成,模具在终锻时受到频繁的冲击和过载,很容易发生早期损坏。实现打击能量数控化,使得设备输出的能量既保证锻件打成,又不产生多余的能量,避免模具打靠产生过载,是提高模具寿命的必经之路。采用数控全液压模锻锤来进行锻造,打击能量和打击工序实现了数控化,下一步就是使用机器人自动上下料,实现自动化生产。因此采用数控全液压模锻锤为主机,实现模锻生产线全自动化生产是下一步的发展趋势。
2.3 数控全液压模锻锤
2.3.1 基本原理
数控锤采用油泵-蓄能器传动,油缸下腔通常压,液压系统对上腔进行单独控制。上腔进油阀打开,来自油泵、蓄能器以及通过差动回路引来的下腔的共三部分高压油进入上腔, 实现锤头的加速向下和打击行程,上腔一旦卸压,锤头立即快速回程。打击能量的精确控制靠数字化控制系统控制打击阀闭合时间的长短来实现。
2.3.2 性能特点
1)能实现打击能量的精确控制。数控锤通过精确控制打击阀的闭合时间, 既保证了锻件所需的能量,又不产生额外的冲击动能,因此锻造模具的寿命大大提高。实测表明,能量偏差控制在±1.5%左右,对于不同高度的模具,可以方便地调整起始时间,保证能量的同一性和准确性。
2)回程速度很快。由于主油缸下腔始终通蓄能器,上腔一旦卸压,能迅速抬锤,因此模具接触时间短,该性能与能量精确控制相结合,可以使锻造模具使用寿命提高2倍以上。
3)锻造精度高。该产品由于导轨采用“X”形结构,因此导轨间隙可以调得很小,打出的锻件精度很高。
4)材料利用率很高。由于能量可以控制,因而制坯精度很高,打出的锻件飞边较为均匀,又由于锻造精度高,上下模不会出现错模现象,因此材料利用率很高,为少无切削奠定了基础。
5)低噪音。由于该产品属打击能量可数控设备,因此编制程序,使锻件打成,但不多给剩余能量,因此噪音很小。传统锻锤的操作者是靠听模具打靠声音来判断锻件是否打成,有时判断不准,习惯于多打几下,实际是多余的。
6)无撞顶现象。通过精确计算和设计液压系统中阻尼孔和节流孔尺寸,使得锤头到顶缓冲下来,很平稳,无一点撞顶现象的发生。
7)低振动。由于该产品打击能量可数控,无多余能量产生,加上锤身下部装有德国技术生产的隔而固品牌隔振器,对周围机床、居民区无任何影响。
8)环保。由于该产品在打击过程中,冲击噪音小,又有减振器,振动小,因而是一种环保型产品。
9)锻件质量较为稳定。由于通过程控器的控制,各种各样锻件的锻造工序可存入程序中,随时根据需要调出来使用, 因此同一种锻件可以得到一致的打击能量和打击次数, 避免了人工操作的多样性,因此锻件质量比较稳定。
10)易于实现自动化生产。由于打击工序和打击能量已实现数控化, 因此为下一步使用机器人自动上下料打下了基础,自动化生产很容易实现。
2.4 锻造液压机的发展过程及发展趋势
锻造液压机是在普通液压机的基础上逐步发展起来的。我国第一台锻造液压机是1953 年在沈阳制造成功的, 开始由于受液压技术和一些液压基础元器件的局限, 锻造液压机的发展是比较缓慢的。近十几年来,由于液压技术的不断发展,锻造液压机进入了一个高速发展期。在2000 年以前我国万吨以上压机不足10 台,仅2006 年一年,投资兴建的万吨压机就有17 台,2007 年投资10 台,两年的投建台数就超过了建国以后五十年的发展, 中小吨位的锻造液压机的需求更是远远大于万吨以上液压机的需求,目前我国锻造液压机的数量大约有200 余台。
锻造液压机发展到现在, 下一步发展趋势就是两个:一个快速性,另一个就是数控联动化。
2.4.1 快速性。目前国外的锻造液压机基本上都是快锻机,快锻次数可达到每分钟100 次以上。特别是适合锻造温度区间很小的高合金材料。在自由锻设备中被认为是发展的主要方向之一。制造快锻机最大的技术难题就在于克服快锻过程中的液压冲击及噪音。
2.4.2 数控联动化。通过采用数控系统来控制锻造液压机的液压系统,实现设备工作智能化,从而实现精密定程压制和定压压制。主机和操作机通过计算机控制,可实现联动。极大地提高了生产效率,锻件精度也有很大程度的提高,锻件成本可得到有效控制。
山东一然环保重视技术创新,加大科技投入,深化改革,加强管理,经过数十年的发展,中国的锻造上了一个新的台阶,天然气锻造炉、热处理台车炉等环保设备的研发生产制造中,以节能增效为主要发展目标,在增强自主开发能力、节约能源、加速发展精密成形等方面都取得了可喜的成果。希望在21世纪能有更多完全国产化的先进技术装备进入锻造业,努力实现全面的锻件净成形,使我国尽早步入世界锻造技术强国之林。